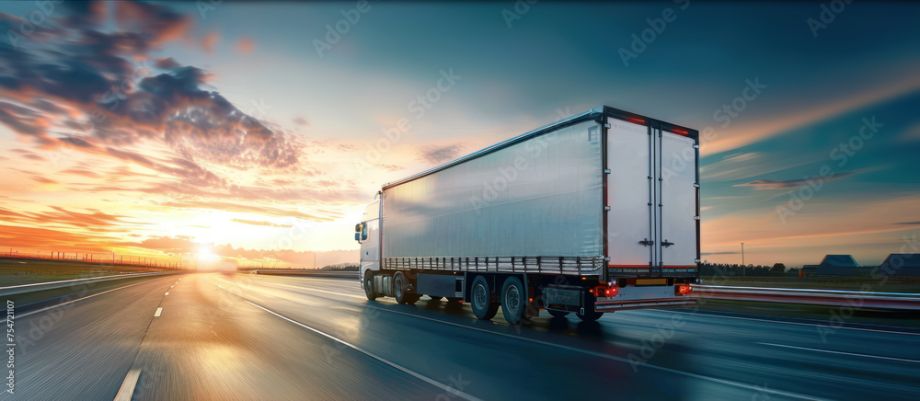
Just-In-Time-Lieferung
Das Material wird so bestellt, dass es exakt zu dem Zeitpunkt eintrifft, in dem es verarbeitet wird. Durch die termingetreue Lieferung wird teure Lagerhaltung abgebaut und Kapitalbindung vermieden.
Für eine Just-in-time-Produktion müssen folgende Voraussetzungen gegeben sein:
- geringe Bedarfsschwankungen
- gleichbleibende Fertigungszeiten
- niedrige Rüstzeiten
- hohe Qualitätssicherung